12 minute read•Updated 4:53 PM EDT, Sun March 31, 2024
[youtube https://www.youtube.com/watch?v=XDsjUtLsuVQ]
Rocket Factory Augsburg (RFA) is a new name in the spaceflight industry that you've probably heard a lot over the past few years. If you haven't, we've got you covered! Back in March, TLP was given the opportunity to have an interview with RFA's Chief Operating Officer and Co-Founder, Dr. Steffan Brieschenk, who talked to us about RFA's Background, engines, facilities, future and more.
Background
RFA is a German based launch provider, established in 2018, their mission is to "democratise space and reduce launch costs in the space industry." They aim to do this by creating a "super competitive launch vehicle (RFA-One) that, while smaller than most, can lift more than 1 tonne of payload into orbit for a very competitive price". They currently have over 200 employees from 40 different nationalities, thanks to the advantages of operating in Europe which has less restricting regulations on employing talent from other countries. Because of this wide variety in backgrounds, RFA finds it important that they operate 100% in English, "so as long as you can speak English and know your engineering you can come here and develop RFA-One with us." This makes operating out of Germany a true advantage, as you can get around without having to speak German and can hire talent from all over the world to "result in the best engineering and best products possible".
Development
RFA is taking a rather unique approach to development, going a similar route to an automotive company, using an already established automotive supply chain. Steffan Brieschenck took us through the decision to take this approach and its benefits.
There is only a business case for a small launch vehicle if you're; A. Not too small, if you can't put 1 tonne into orbit, the business case will likely not resolve. B. Even if you have something that can deliver at least 1 tonne, it's still going to be very hard to compete with the bigger launch vehicles that have a higher payload mass fraction, if you do not produce in an automotive like fashion, where you can really bring down the cost through mass production. Because of this, RFA uses more suppliers from the automotive industry than the aerospace industry, which not only drastically reduces the cost, but also completely changes the production timeline.
When RFA began designing the RFA-One vehicle, they started with the propulsion system, the Helix engine, which was named by the public via an online vote. 9 of these engines will power the first stage of RFA-One while a single vacuum optimised Helix will power the second stage. The first prototypes of the helix engine are capable of producing 10 tonnes of thrust and currently take between 3-6 months to develop. In the future, RFA wants to resolve their supply chain to drastically reduce this production time frame to a couple of engines being produced per day, they hope to
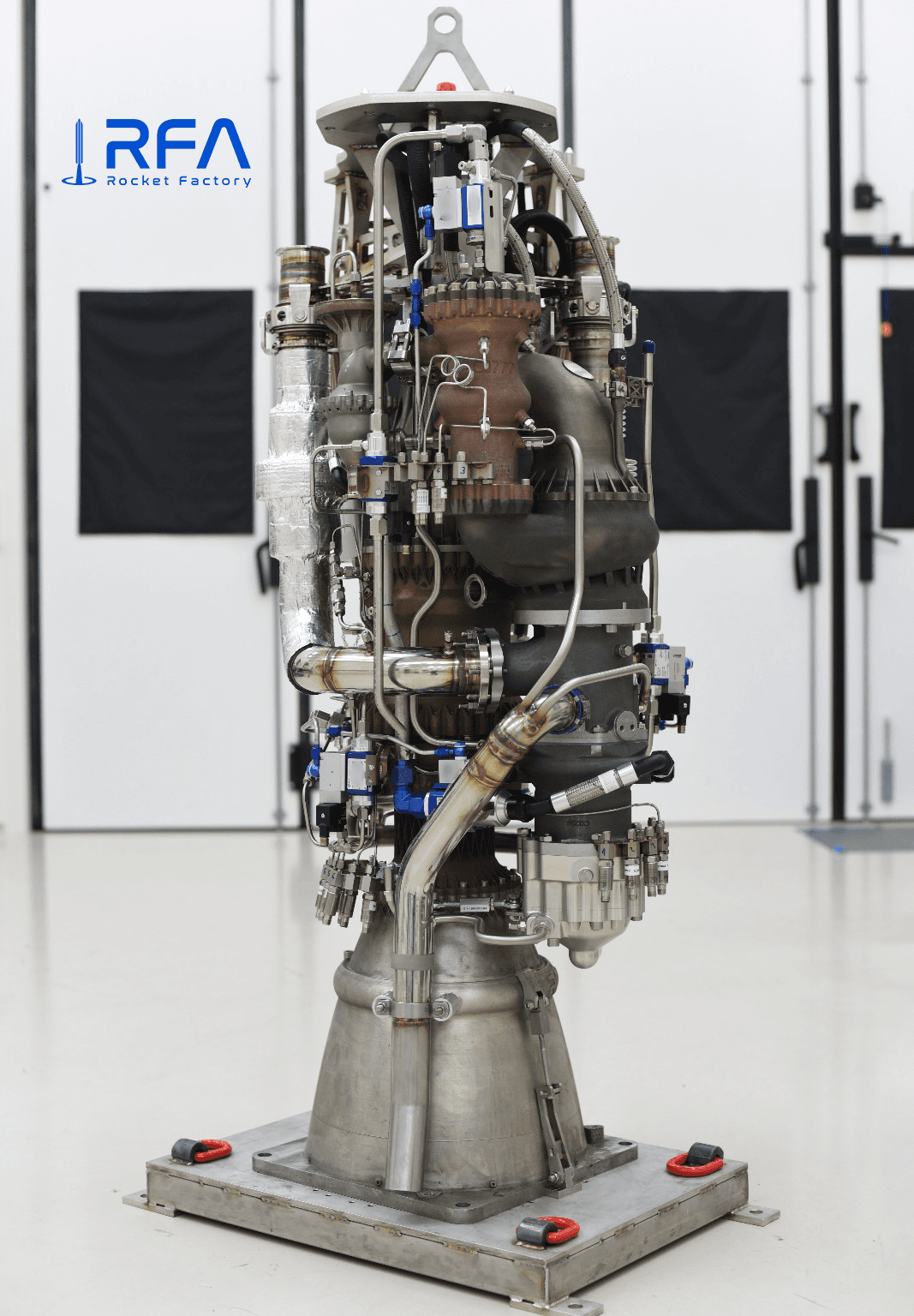
achieve this by producing their engines in a similar way an automotive company would produce an engine, which would also help reduce the cost of each engine, which currently costs about the same amount as the entire stage. Originally, Helix was planned to be a gas generator cycle engine, but in 2020, RFA switched to a Oxygen rich staged combustion cycle engine. RFA made this change after using an optimiser, which used many parameters to find which engine configuration, stage configuration, and manufacturing methods would result in the best payload to orbit in terms of cost. Initially, RFA was reluctant to pursue the stage combustion engine, since one had not been developed en masse for a small launcher before, so they decided to produce 2 different types of engines on paper, before finally deciding to take to stage combustion cycle approach, which they have now developed into Helix.
The first helix prototype was made from parts from various suppliers, with the combustion chamber being developed in house, when it came to testing this prototype, there was concern about the combustion chamber dissolving and falling apart during startup and shutdown, as is common with stage combustion cycle engines. However, the engine survived the test! With the data gained from the tests, RFA went to the drawing board to modify the design so that it could produce 10 tonnes of thrust while being as slim as possible, to allow for clustering. This design was then assembled and tested in Sweden, where it was fired for a duration of 74 seconds and they currently have a Helix vacuum engine attached to an upper stage prototype in Sweden awaiting its hotfire test. This is where RFA stands currently, as they build more Helix engines for further testing and flight certification.
As for RFA-One's third stage, called Redshift, RFA decided to take a unique approach in that it is a hybrid orbital insertion stage, providing the last necessary amount of ΔV needed to achieve orbit, and an orbital transfer vehicle. This decision once again goes back to the optimiser that RFA ran.
Since they wanted an orbital transfer vehicle that can stay on orbit for a long time, a lot of thought went into which propellants to use on the stage. They wanted to ensure that the propellants would not boil off in space, but also that they were safe to use, since the occupational health and safety measures associated with more dangerous fuels, such as Hydrazine, end up costing a lot of money. So, RFA settled on using a green propellant for the Redshift stage, which can be stored for more than a year on orbit. Redshift is also a very flexible stage, offering both primary and secondary payloads on a single mission, with the ability to have orbit raising and inclination changes to meet the customer's needs, some customers even have interest in using Redshift as an orbital stage after its primary mission, performing science/observations in one area and then changing its position to perform them in another area.
Another long term aspect of RFA-One that has been designed from the beginning is fairings. RFA-One will have 3 different fairings for customers to choose from, and were all designed at the same time as designing fairings for an in development launch vehicle is much easier than designing fairings for a launch vehicle that is already in opertaion. So RFA decided to design all 3 of their fairings together from the start. for the first flight, they have chosen to use the simplest fairing design so they can decrease the complexity margins.
Re-Use
Currently, Helix has a set amount of times it is capable of restarting, so that it can be hotfired for certification testing, and then also carry out its mission. This is due to the previously mentioned risks during startup and shutdown of Oxygen staged combustion cycle engines, but in the future, RFA would like Helix to be infinitely restartable so that they could pursue re-use of the RFA-One vehicle, which would drastically cut the cost of engine production and reduce the launch cadence to (ideally) once a week. Currently, RFA likes the idea of using parachutes for re-use, but notes the challenges of opening parachutes at high speeds and reliability, so they are currently not focusing on re-use but instead getting their first rockets to orbit, but have concepts, partners and studies for the future.
Facilities/Launch Locations
RFA operates three facilities across the globe, they mainly operate out of their headquarters in Augsburg, South Germany, the heart of the German automotive industry. This is where a majority of their staff are located and where most R&D and testing takes place. RFA had initially wanted to also test their engines in Germany, however were unable to receive approval at the time. So, they instead currently test at a facility in Sweden which has its own small dedicated team. This has proven to be a logistical problem for them, however, due to transport and weather being inconvenient. Because of this RFA plans to move their testing facility to Germany in the near future, having recently received an agreement to test in Germany. Besides these two facilities, RFA also has a facility in Portugal focused on the fabrication of composite parts and have started moving some of their staff to the UK as they begin to prepare for their maiden launch. In the future, RFA hopes to open factories in more locations across the world to once again reach their vision of operating like an automotive company, which also have factories in multiple locations across the globe. This would also help to increase the launch cadence as not every rocket would need to be shipped from Germany, but could instead be built closer to the launch location.
Currently, RFA is looking to launch their rockets at Saxavord Spaceport, located at the northern-most tip of the Shetland Islands in Scotland. The decision to launch from these locations was an opportunistic one, RFA had to look at the best locations in terms of best commercial deal and lowest technical risks. These decisions have to be made quickly, since these deals won't last for long, so they have to make sure they are making the right decision. So after assessing all the commercial, techincal and political risks, RFA decided the best location for launching would be the Shetland Islands.
Some of the benefits of launching from the Shetland Islands that appealed to RFA were the large flight termination corridors, since there is a lot of open water with very little air or sea traffic in the area, making it ideal for a first launch location, since statistically, a lot of first launches unfortunately fail. Because of this, a lot of spaceports don't like to host maiden launches, so RFA had meetings with multiple spaceports around the world, and the meetings in the UK had the best outcome, so the decision was made to launch from there. RFA is excited to move their first stage to the Shetlands for hotfire testing and launch later this year.
Flight 1
the first 3 Helix engines for flight 1 are currently complete, and a batch of 12 more engines are in production. The second stage prototype, which they hope to use for flight 1 if everything goes well, is currently undergoing numerous hot fire tests in Sweden to verify the total impulse and efficiency of the ISP of the engine (including the startup and shutdown). Once that is completed, they will switch their focus to performing similar tests with the first stage, which is currently in the final integration phases at their factory in Augsburg. The fairing and composites for the Redshift stage are currently being assembled and are on track to be completed this year. RFA plan to ship the stages and engines separately to the Shetland Islands in containers and then integrate them there, to reduce complexity and the risk of damage, later this year. This has been achieved by making the interfaces simplistic, so a vehicle can be put together and torn apart as quickly and easily as possible. For example, each engine is designed so that it can fit into any engine position on the first stage, instead of being allocated to a certain position, which helps to keep the engines small and uniform. RFA won a competition to fly multiple payloads on their first launch, and they have already set their configuration, now all that's left to do is complete the testing and launch their first flight as soon as possible.
The future
RFA is focusing on how best to compete in the launch market, instead of competing with other small launch vehicles, they have decided to compete directly with larger launch vehicles on a price per KG basis, they are aiming to launch payloads into space for a price of $5,000 per KG but would reduce that price, depending on demand, to whatever makes commercial sense. RFA can currently tolerate at least a single launch failure, however this is not an issue as they plan to get the RFA-One functioning as soon as possible. They get funding from their main backing investor, a satellite company, which provides them payloads, as opposed to capital. So once RFA-One is operational they will have a steady income from the payloads that they have signed on to launch. This has allowed RFA to focus far more on the engineering side of the company than the financial side, unlike other startup companies that have to deal with things such as venture capital as well as development.
As RFA continues to expand, they have more and more positions opening, and Steffan Brieschenk encourages anyone who is motivated and has an engineering mind to come and join them at RFA, including younger people who have just left University and are looking to have a career in the aerospace industry and want to be part of the revolution in spaceflight RFA is building. You can apply to work at RFA on their careers website or if you want to follow RFA's progress and engage with the team, you can follow RFA on their social media pages.
Thank you to Dr. Steffan Brieschenk for taking the time to give us this interview, we wish him and the whole of the Rocket Factory Augsburg team good look on their maiden flight of RFA-One, and their future endeavours beyond!