LAUNCH CENTER
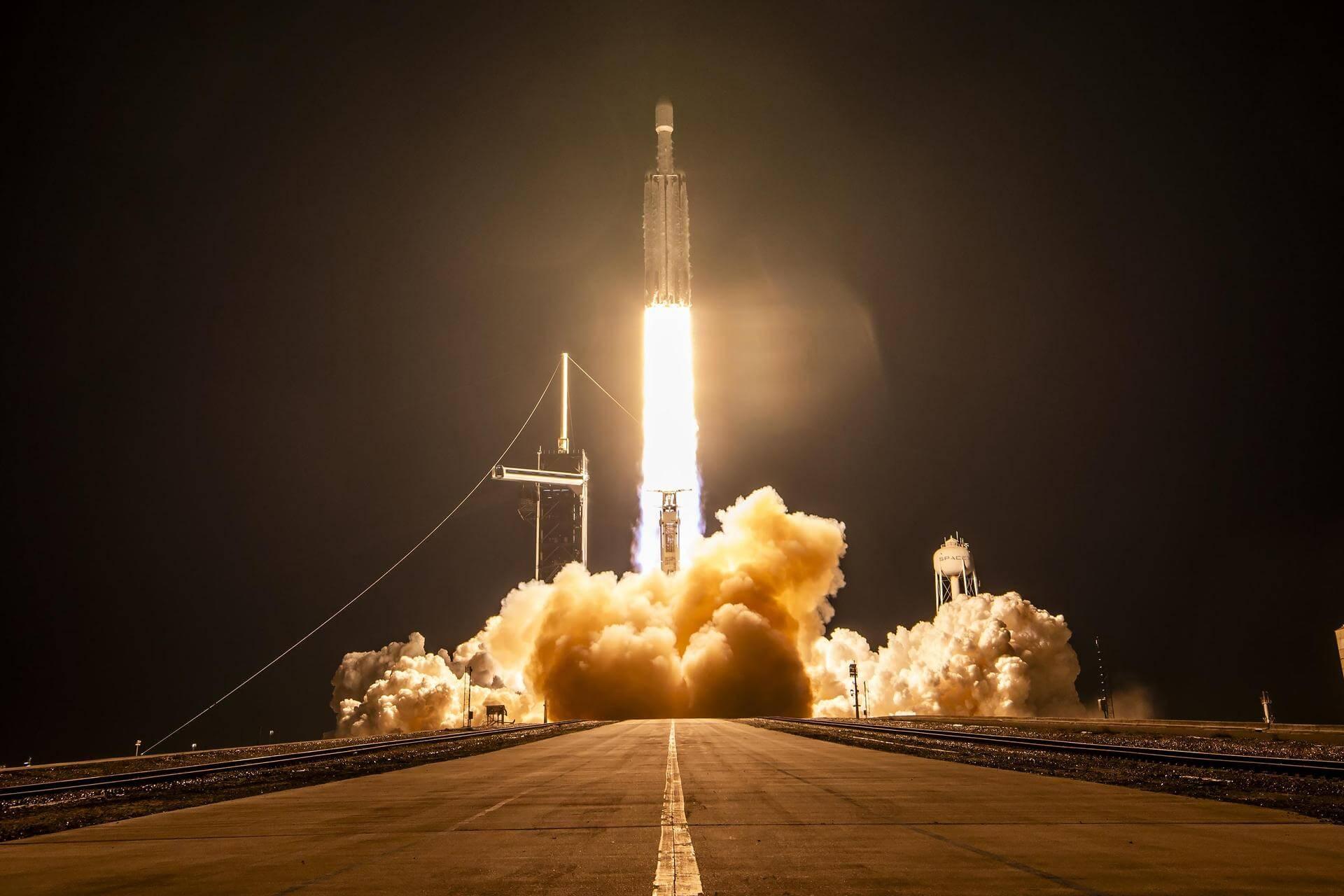
Success
Fri Dec 29 2023
SpaceX
Mission TBD
Launch Successful
LAUNCH TIME
Loading...
(Loading...)
Loading...
Window Open
Loading...
(Loading...)
Window Close
Loading...
(Loading...)
RECOVERY OVERVIEW
Location
No Recovery Specified
Type
No Recovery Specified
Rocket Details
Name:
Falcon HeavyDescription:
The Falcon Heavy is a variant of the Falcon 9 full thrust launch vehicle and consists of a standard Falcon 9 rocket core, with two additional boosters derived from the Falcon 9 first stage.
MISSION OVERVIEW
- Type:
COMPLEX OVERVIEW
Location
Kennedy Space Center, FL, USA
Pad
Launch Complex 39A